A 5 MW project for British Sugar
British Sugar uses sugar beet pulp to generate heat and electricity
Facts & figures
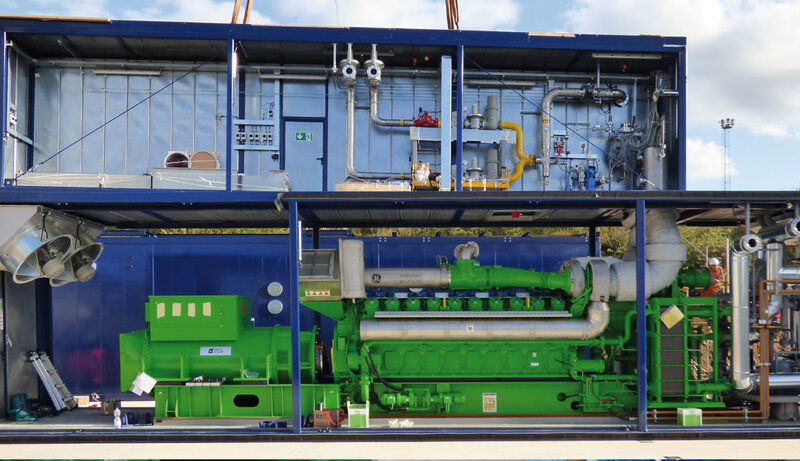
British Sugar is a leading processer of sugar in Great Britain and produces around 1 million tons of sugar in the UK, and 500,000 tons of animal feed products from sugar beet pulp.
Combined Heat and Power (CHP) technology is a significant part of their daily business, with existing CHP operations at each of their 4 operational beet processing sites in the UK. The CHP at Wissington factory also supplies hot water and excess carbon dioxide to greenhouses at Cornerways Farm to help grow over 140 million tomatoes each year.
British Sugar has recently invested in an AD plant at their Bury St. Edmunds, using sugar beet pressed pulp to feed the digesters and generate biogas, to fire two 2G CHP gas engines; helping to provide 8,000 households with electricity.
The two CHP units were installed in two containers with the considerable size of 35.00 x 13.60 x 8.80 m.
Each of the two containers consists of 6 sections:
1. Engine (avus 2000b and avus 3000a)
2. Heat extraction
3. Gas control line with compressor unit
4. Ventilation system with air filter
5. Control system and oil tanks
6. Medium voltage system with connection to the public grid.
The installed CHP gas engine plants are an avus 3000a with an electrical and thermal output of 2.8 MW, and an avus 2000b with an electrical and thermal output of 2.2 MW. The total efficiency of both plants is approximately 86%, which is significantly higher than commercial fossil fuel power plants.
The gas engines were designed, manufactured and tested in Germany. After being dissembled, the separate container sections were transported on trucks to the UK, where they were installed and commissioned within 30 days.
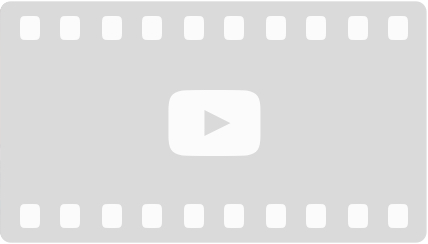