Waste management and energy production in one
One of the largest duck farms in North America disposes its organic waste with three agenitor
Facts & figures
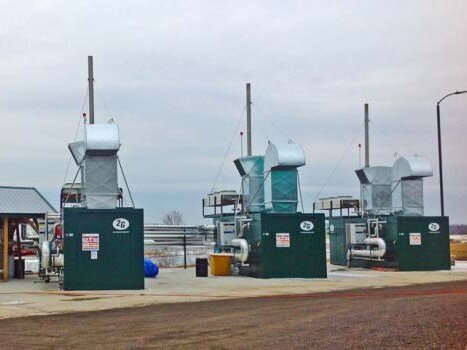
This large CHP system owned by one of the largest duck farms and processing facilities in North America, is located outside of Middlebury in Indiana. The customer processes in excess of 6.5 million ducks annually. All ducks are raised on satellite farms in the surrounding area. In 2011 the company broke ground on an anaerobic digester to manage the 18,000 lbs/day of duck droppings and offal generated in its processing plant.
The 2G CHP scope and installation consists of 3 x fully sound attenuated containerized CHP modules with each housing a 2G agenitor 212 engine as prime mover. The electrical capacity per unit is 400ekW/h, which provides a total of 1,200 ekW per hour or a total of 9,960 MW/h per year, which is sold to the local utility company under a 15-year power purchase agreement (PPA). The thermal heat produced is 1,422 kwh/th. This valuable thermal energy is used to heat processing water at the farms facility, the processing plant, and the digester facility itself. In the past the farm had to find ways to dispose all organic waste. The 942,000 gallon capacity digester is designed for, and will utilize the large amount of duck offal combined with corn silage and other substrates for the production of high quality biogas to be used for all three CHP modules. The biogas is first treated and cleaned using a 2G Gas Treatment System consisting of biogas dehumidification for moisture removal before it enters the combustion process for the engine. An additional 2G H2S filtration system was added. The entire power generation process is monitored 24/7.