Recyclage durable
Outre les snacks, l'usine Lorenz Snack-World, située dans la ville bavaroise de Neunburg vorm Wald, produit des déchets et des matières résiduelles qui sont entièrement transformés en énergi
Faits et chiffres
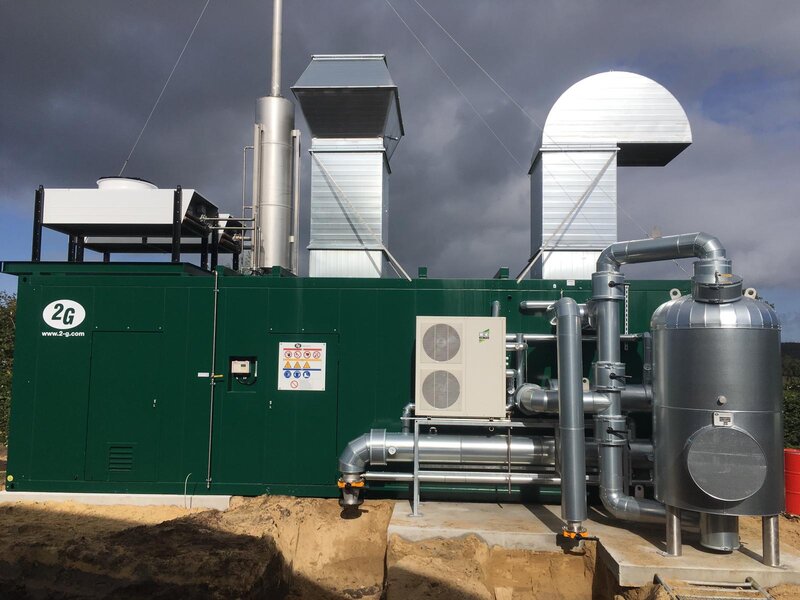
Qu'il s'agisse de chips ou de boulettes de cacahuètes, si vous grignotez en Allemagne, elles proviennent peut-être d'une petite ville de Bavière : Neunburg vorm Wald. L'usine Lorenz Snack-World de cette ville produit chaque jour de grandes quantités de snacks, mais les chips et les boulettes de cacahuètes ne sont pas les seuls produits qui sortent de l'usine. L'usine produit également des déchets et des matières résiduelles, principalement des pelures de pommes de terre et des eaux usées provenant du processus de lavage des pommes de terre. Dans ce cas, toutefois, le terme "déchets" n'est pas synonyme de "gaspillage" : Lorenz transforme les déchets biologiques et même les eaux usées en énergie. À cette fin, l'entreprise a construit des réacteurs à gaz d'égout et à biogaz à proximité de l'usine.
Ce complexe contient également un système de production combinée de chaleur et d'électricité qui a été mis à niveau en 2021. Grâce à ce système de cogénération, l'entreprise peut couvrir 17 % de la demande en électricité de l'usine - un pilier de la stratégie générale de durabilité de Lorenz. Mais même les matières résiduelles qui ne peuvent pas être transformées en énergie sont recyclées : les eaux usées de l'usine contiennent d'importantes quantités d'amidon qui doivent être filtrées. Après quelques processus, cet amidon peut être réutilisé dans la production. L'eau nettoyée et filtrée est à son tour réutilisée pour prélaver les pommes de terre non épluchées.
Bien que le siège du groupe familial Lorenz se trouve en Hesse, les trois usines allemandes de l'entreprise sont situées en Bavière, en Basse-Saxe et en Saxe. Selon son dernier rapport sur le développement durable, l'électricité verte produite dans les parcs éoliens et les centrales hydroélectriques couvre déjà la demande de la plupart des usines et des infrastructures administratives de l'entreprise. L'entreprise a l'intention de couvrir entièrement la demande d'électricité de tous ses sites avec de l'énergie renouvelable d'ici 2023.
Des déchets au biogaz
L'usine de l'est de la Bavière est entrée en service en 1968. En 1993, Lorenz a ajouté une station d'épuration des eaux usées à l'installation et en 2005, ils ont non seulement ajouté un système de conversion des déchets en biogaz au complexe, mais 2G Energy a également installé un système de production combinée de chaleur et d'électricité pour convertir le biogaz en énergie directement sur le site. En novembre 2021, il était temps de moderniser le système de cogénération. 2G Energy a installé un "agenitor 412" conteneurisé à côté de l'usine de biogaz. Le système a une puissance de 404 kW d'énergie électrique et de 474 kW d'énergie thermique et est équipé d'un catalyseur d'oxydation. Chaque année, la cogénération produit environ 2,3 millions de kWh d'énergie électrique et 2,5 millions de kWh d'énergie thermique.
L'usine de snacks ne cesse de produire des déchets compostables et des matières résiduelles, de sorte que la production de biogaz et d'énergie par la centrale de cogénération ne s'arrête pas non plus. "Nous convertissons 100 % de nos flux de déchets dans l'usine. La cogénération est suffisante pour cela", explique Thomas Beer, responsable du service de traitement des eaux usées de Lorenz. Pour lui, ce concept énergétique se double d'une stratégie de réduction des coûts : l'entreprise évite de payer des frais élevés pour l'élimination par des tiers ainsi que pour le transport vers le site d'élimination, ce qui rend la stratégie de recyclage non seulement plus durable, mais aussi plus rentable que les méthodes traditionnelles.
L'un des principaux piliers de la stratégie consiste en fait en deux piliers distincts. L'usine de biogaz contient deux réacteurs aux caractéristiques distinctes. Le premier transforme en biogaz les déchets solides, tels que les épluchures et les résidus de pâte produits par l'usine, tandis que le second convertit les matières plus liquides. Le second réacteur utilise la technologie UASB (upflow anaerobic sludge blanket) adaptée à la digestion des déchets particulièrement liquides, comme l'eau qui a été utilisée pour laver les pommes de terre. Chaque année, les réacteurs combinés produisent environ 1,1 million de mètres cubes de biogaz.
L'électricité cogénérée est utilisée pour la production
En aval des réacteurs, les deux gaz sont accumulés et mélangés. Le mélange de gaz est ensuite séché et désulfuré avant d'être utilisé pour alimenter le système de production combinée de chaleur et d'électricité - cogénération d'énergie thermique et électrique. "La chaleur reste dans le complexe et est consommée sur place", explique M. Beer. Outre les réacteurs doubles, le système de Neunburg vorm Wald présente une autre caractéristique unique : "Des quantités considérables d'amidon sont éliminées lors des processus de lavage et d'épluchage. Comme il doit de toute façon être filtré dans les eaux usées, nous avons décidé d'aller plus loin en raffinant l'amidon récupéré jusqu'à ce qu'il puisse être réutilisé", explique M. Beer. La réutilisation de l'amidon et de l'eau filtrés, tout en évitant l'achat de ressources supplémentaires, est une autre combinaison de durabilité et de rentabilité.
Quant à l'électricité produite par la cogénération, elle est entièrement utilisée pour la production dans l'usine. Pour faciliter l'utilisation de l'électricité, le système de production a été connecté directement au réseau de l'usine en novembre 2022. L'installation est complétée par une centrale énergétique avec des systèmes de production de vapeur, des compresseurs, des transformateurs et d'autres systèmes auxiliaires. Lorenz a également signé un contrat de service complet avec le fabricant de centrales de cogénération 2G Energy. "S'il y a des dysfonctionnements, nous voulons qu'ils soient détectés le plus tôt possible", explique M. Beer pour expliquer la décision de l'entreprise de laisser les employés de 2G surveiller le système 24 heures sur 24 afin qu'ils puissent intervenir si nécessaire. En cas d'arrêt du système, par exemple lors d'une opération de maintenance, les déchets et les matières résiduelles peuvent toujours être collectés, mais l'arrêt ne doit jamais durer trop longtemps. C'est pourquoi Lorenz a même loué une centrale de cogénération pendant le processus de modernisation. Dans l'ensemble, Thomas Beer est satisfait du système. Il considère que les deux arguments qui ont conduit à la coopération avec 2G Energy, à savoir la fiabilité et une certaine échelle organisationnelle, sont remplis. Le montant investi par 2G pour le nouveau système de production combinée de chaleur et d'électricité, y compris les composants et les interfaces, s'élève à environ 500 000 euros.