Green energy for beans and tomatoes
Susquehanna River Valley's premier grower and producer of beans and tomatoes opts for 2G
Facts & figures
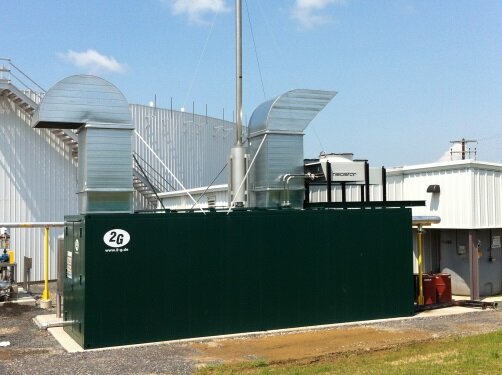
A well know food processing plant located in Northumberland, PA, is the Susquehanna River Valley's premier grower and producer of beans and tomatoes. Increased production in recent years meant that the company's on-site wastewater treatment system required upgrading and expansion. Additionally, in keeping with its environmental commitments, the customer was interested in generating green energy from its wastewater. ADI was awarded a contract to design and build the anaerobic system for digestion of organic wastes, along with supplying a highly efficient biogas CHP system for production of electricity and thermal energy from the biogas produced by this new digester.
The CHP cogeneration plant consists of a 2G patruus 250 with integrated MAN engine capable of producing 250 ekW/h or 2,075 MW p.a. Electrical Power and 322 kWh/th Thermal Power, all built in a 30' sound attenuated CHP container module. Additionally 2G Energy Inc. installed a complete gas treatment system, including biogas, dehumidification & reheating system, and the double vessel H2S removal technology. The customer's wastewater flow and and volume vary considerably throughout the year. Therefore it was important that the system is able to accommodate fluctuations in load, yet maintain consistent performance and maximize biogas utilization. The anaerobic system designed by ADI consists of a 7.5 MG ADI-BVF® reactor, complete with internal in-fluent/effluent distribution piping, mixer, biogas collection/handling, and a sophisticated, yet simple, graphics-based computerized monitoring and controls system. During periods of peak biogas production, the excess biogas is burned in a high-efficiency enclosed flare. The plant, commissioned in February 2012, is designed to treat a peak flow of 1.06 mgd with chemical oxygen demand / biochemical oxygen demand (COD/BOD) concentrations of 5800/3400 mg/l, providing better than 85 percent COD and 90 percent BOD reduction.

