Sustainable Recycling
Besides snacks, the Lorenz Snack-World facility in the Bavarian town of Neunburg vorm Wald produces waste and residual materials that are entirely converted to energy.
Facts & figures
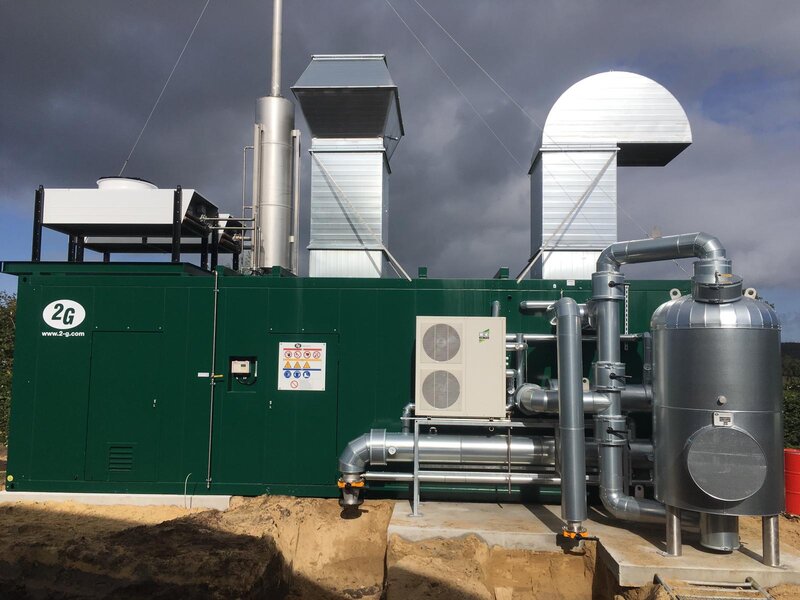
That complex also contains a combined heat and power generation system that was upgraded as recently as 2021. With this dedicated CHP, the company can cover 17 percent of the factory’s electricity demand – a pillar of the general sustainability strategy at Lorenz. But even residual materials that cannot be turned into energy are still being recycled: the factory’s wastewater contains significant amounts of starch that must be filtered out. After a couple of processes, that starch can be reused in production. In turn, the cleaned and filtered water is reused to pre-wash the unpeeled potatoes.
Although the headquarters of the family-owned Lorenz Group are in Hesse, the company’s three German factories are located in Bavaria, Lower-Saxony, and Saxony. According to their latest report on sustainability, green electricity produced in wind parks and hydroelectric facilities already covers the demand of most of the company’s factories and administrative infrastructure. The company intends to cover the electricity demand of all its locations entirely with renewable energy by 2023.
From waste to biogas
The factory in Eastern Bavaria took up operation in 1968. In 1993, Lorenz added a dedicated wastewater treatment plant to the facility and in 2005 they not only added a system to convert waste into biogas to the complex, but 2G Energy also installed a combined heat and power generation system to convert the biogas into energy right on site. In November 2021, it was time to upgrade the CHP. 2G Energy installed a containerized “agenitor 412” alongside the biogas plant. The system has an output of 404 kW electrical energy and 474 kW thermal energy and is equipped with an oxidation catalyst. Annually, the CHP produces about 2.3 million kWh of electrical and 2.5 million kWh of thermal energy.
The snack factory never stops producing compostable waste and residual materials, so the biogas and energy production by the CHP do not stop either. “We convert 100 per-cent of our waste flows in the facility. The CHP is adequate for that,” says Thomas Beer, head of the wastewater treatment department at Lorenz. To him, this energy concept doubles as a cost-saving strategy: the company avoids paying hefty fees for the disposal by third parties as well as the transport to the disposal site, making the recycling strategy not only more sustainable but more profitable than traditional methods.
One of the strategy’s main pillars, actually consists of two individual pillars itself. The biogas plant contains two reactors with distinct features. One reactor turns the solid waste, such as peels and dough residues produced by the factory, into biogas, while the other converts the more liquid materials. The second reactor uses UASB (upflow anaerobic sludge blanket) technology tailored to the digestion of particularly liquid waste – like water that has previously been used to wash potatoes. Annually, the combined reactors produce about 1.1 million cubic meters of biogas.
Cogenerated electricity used for production
Downstream of the reactors, the two gases are accumulated and mixed. Then, the gas mixture is dried and desulfurized before being used to fuel the combined heat and power system – cogenerating thermal and electrical energy. “The heat remains on the complex and is consumed on site,” explains Beer. Besides dual reactors, the system in Neunburg vorm Wald has another unique feature: “Staggering amounts of starch are rinsed out during the washing and peeling processes. Since it must be filtered out of the wastewater anyhow, we decided to go one step further by refining the recovered starch to a point where it can be reused,” explains Beer. Another combination of sustainability and cost-efficiency in reusing the filtered starch and water while avoiding the purchase of further resources.
As for the electricity generated by the CHP, it is used entirely for production in the factory. To facilitate the use of electricity, the generation system was connected directly to the factory’s grid in November of 2022. The facility is rounded out by an energy central with systems for steam generation, compressors, transformers, and other auxiliary systems. Lorenz also signed a Full-Service contract with the CHP manufacturer 2G Energy. “If there are any malfunctions, we want them to be detected as early as possible,” Beer explains the company’s decision to let 2G employees monitor the system around the clock allowing them to intervene whenever necessary. If the system is ever shut down, during maintenance for example, the waste and residual materials can still be collected, but the standstill must never last too long. Therefore, Lorenz even rented a CHP during the upgrading process. Overall, Thomas Beer is satisfied with the system. He considers the two arguments which led to the cooperation with 2G Energy, namely reliability and a certain organizational scale, to be fulfilled. The amount invested for the new combined heat and power system by 2G including the relevant components and interfaces adds up to approximately 500,000 Euros.