Repeat purchases out of conviction
Significant energy savings in the meat production at Manten
Facts & figures
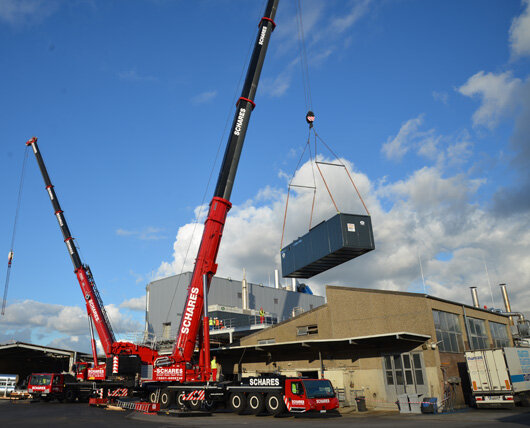
If you ask the entrepreneur Heiner Manten why he bought a second, even bigger combined heat and power system by 2G only two years after his first was commissioned, his answer is short and simple: "To be honest, I was simply convinced by what the Bajorath Systemhaus and 2G do as a team.“
No wonder: Trending towards a drastic decrease in energy costs and CO2 emissions after only a year, the meat producer Heinrich Manten is projected to save about half a million Euros per year, thanks to the solution for combined heat and power production developed by Bajorath Systemhaus.
From the Lower Rhine into the world
The middle-scale family business, Heinrich Manten Qualitätsfleisch vom Niederrhein GmbH & Co. KG, successfully combines tradition and innovation. Founded by the master butcher Heinrich Manten in 1951, the company located in Geldern on the Lower Rhine is now managed by the brothers Heiner and Peter Franz Manten, the second generation of the founding family. More than 450 employees work at the original location in Geldern which has become highly technologized. There they produce, package and store pork. Up to 100 tons of fresh meat can be shock-frozen in the state-of-the-art refrigerating and freezing facility every day. Manten mostly distributes the products to customers within Germany and the EU, but the company also distributes to the Asian market: to specialized butcheries, restaurateurs but also to meat processing businesses and the meat wholesaling sector.
Sustainable production
In 2016, Manten tasked the Bajorath Systemhaus für Regelungstechnik und Hydraulik GmbH from Osnabrück with the elaboration of a holistic energy concept covering the production as well as the utilization of energy. During the same year, the first combined heat and power system was put into operation in Geldern to be a key element of the energy concept: an agenitor 312 by 2G with an electrical output of 450 kW and a thermal output of 468 kW.
Highly efficient combined heat and power systems
By choosing an agenitor 312 by 2G as its first CHP, Manten did not only choose to increase efficiency and decrease CO2 emissions, but to become independent of external electricity as well. The desired impact on the energy costs and the CO2 balance in particular, quickly became evident. Therefore, the Manten brothers did not have to think long about getting a second CHP. Especially since this new plan was not limited to an expansion of decentralized electricity generation but included a complete overhaul of the cooling supply concept for the refrigerating and freezing facility. Due to their positive experience with the agenitor, they wanted to acquire another 2G system – but bigger. They decided in favor of an avus 500b with ab electrical output of 637 kW and a thermal output of 739 kW – to be combined with an absorption refrigerating machine. But where to set up the new system? Appropriate, level surfaces were either not available due to a number of legal restrictions or because they were set aside for future expansions of production capacities.


Smart set-up solution
Bajorath Systemhaus had the solution: the erection of a 375 square meter steel platform weighing 86 tons directly intended to accommodate the entire energy and refrigerating technology next to the production facility. An ideal solution that also entailed four advantages:
- Simple hydraulic connection of both CHP to the absorption refrigerating machine
- Easy access for oil changes, inspections, and system overhauls
- Compliance with fire safety requirements and all further relevant structural engineering norms
- Short lines from the absorption refrigerating machine to the refrigerating and freezing facility to supply cooling
Conversion during non-production weekend
The relocation of the agenitor 312 onto the platform and the installation of the avus 500b were scheduled for the last weekend of October 2018, so that no production processes would be disrupted during the business week. The supply lines – electricity, gas, water – were installed beforehand. On that weekend, two cranes lifted the agenitor 312 inside its container from its old location onto the steel platform. It was able to resume operation no later than Monday morning – as soon as production started. That same weekend, the second container containing the avus 500b was also placed on the platform and it was commissioned only a few weeks later.
Quickly available, thanks to Plug & Play
Quick and easy relocations as well as short installation times are made possible by the Plug & Play container solution concept by 2G. At the 2G factory in Heek, the container is installed inside a container and tested, so that the customer merely has to prepare the interfaces for the supply of electricity, gas and water. Therefore, a commissioning even after only a few days is common.
2G offers containerized solutions in many variants – even with acoustic insulation. With the corresponding noise protection package, the noise emission does not exceed 45 dB (A) at 10 m.
Substantial energy savings
The agenitor 312 and avus 500b provide the Heinrich Manten facilities with electricity and heat, with the former being consumed directly by the company and not fed into the public grid. The heat is temporarily stored in a buffer tank and fed into the absorption refrigerating machine or the heating system as required.
Both CHP are projected to save more than 350,000 Euro in annual electricity costs. The approx. 110,000 Euro that Manten is not spending on grid tariffs, thanks to production‘s self-sufficiency, can be added to that. According to current projections, switching the absorption refrigerating machine from electricity to heat will likely save 70,000 Euro. The avus 500b will have paid off after about 5 years.
Optimal control over the system
To ensure the perfect control over the system and the integration into production processes, BOCS (Bajorath Operating Control System), the system control technology developed by Bajorath, is being used. At the core of this technology are several interconnected control cabinets, one of whom has been equipped with a 21.5“ touchscreen display which does not only ensure that the system and production management data can always be read but influenced as well. For a better general overview, the data is being supported by a comprehensive visualization of the system components.
Certified energy data management
The company Heinrich Manten is certified according to DIN EN ISO 50001 and does not only aim high in matters of improving energy efficiency and reducing CO2 emissions. “We are also intent on implementing and living a constant process of improvement through the utmost transparency regarding our energy flow and energy indices“, proclaims Heiner Manten. BECS (Bajorath Energy Control System), the energy data management software developed by Bajorath which the Federal Office for Economic Affairs and Export Control (BAFA) lists as an eligible software solution and which is also certified by TÜV Rheinland, helps to achieve this goal.
Economic efficiency in mind
The perfect symbiosis of the systems BOCS and BECS allow Manten to optimize the system operation at any point in time while also providing web-based access to all data on energy consumption, energy costs and energy indices. Thanks to the software, Manten can also keep an eye on the economic efficiency of the 2G CHP (operating messages, run times, consumptions, electrical and thermal output, utilization ratio, electricity price, grid costs, apportionment for renewable energies, cogeneration compensation etc.). This constitutes the perfect basis for the continued, periodical identification, evaluation, and auditing of Energy Performance Improvement Actions, the so-called EPIAs.