Perfect Synergy of Cogeneration and Heat Pumps
Facts & figures
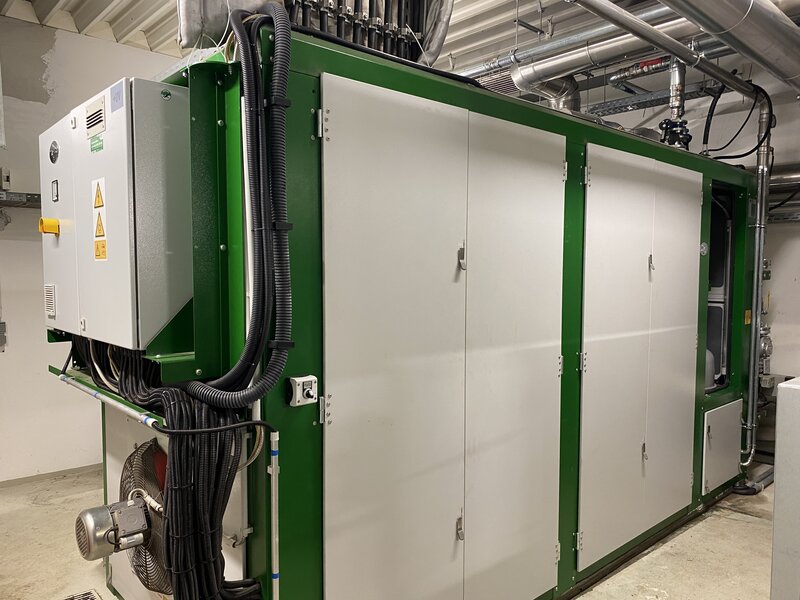
“It is an excellent example of how much sense it can make to combine heat pumps and combined heat and power systems,” says Holger Herzberg about the modernized generation facility for Dreiangel. Herzberg oversees energy production at the Vereinigte Stadtwerke. In 2020, the company began renewing its old cogeneration system, a process that finished with the arrival of the last components in 2023. The innovation at the core of the modernized system lies in its combination of heat pumps with a buffer tank to recover the low-temperature heat of the CHP.
The cogeneration facility supplies the district heating network Dreiangel. The core of the system was completely replaced by a new CHP, two heat pumps and two buffer tanks. The concept exploits the ground source heat pumps in a particularly innovative manner raising the overall efficiency and flexibility of the system. The association of regional public utilities invested around 450,00 Euros into “the modernization of the system, making it fit to face the future,” tells us Herzberg. The facility supplies a district heating network that covers the Dreiangel district with about 200 households, a kindergarten, and a grocery store.
Overdimensioned buffer storage for increased flexibility
Until the modernization, a naturally aspirated 250-kW MAN engine was running tirelessly and without fail. Herzberg on the old situation: “The engine ran in modulating operation between 20 and 250 kilowatts. There was no need for a buffer tank”. In 2019, however, the question arose on how to sensibly modernize the system. Prerequisites were that the new system be adaptable to an expansion of the district heating network and that it can continue to run on biomethane.
Vereinigte Stadtwerke opted for a combined heat and power system by 2G Energy to supply the urban district heating network Dreiangel. Cost-effectiveness was a key factor in the decision, but the electrical efficiency of the new power unit was also a significant upgrade. The CHP has an electrical output of 385 kW and a thermal output of about 400 kW. Herzberg goes into detail: “The system works within the Renewable Energies Act, like the old system, meaning that the electricity is sold via direct marketing. The engine is flexible, runs in different time slices, less during summer, more during winter. Overall, the CHP amasses about 4,500 full-load hours per year.”
Furthermore, the planners insisted that the system be equipped with an SCR catalyst, a system for selective catalytic reaction. SCR systems ensure ideal exhaust gas purification and reduce emissions, making them critical components of CHP systems. “The CHP is complemented by the boiler system and a hefty 50,000-liter buffer tank that is as high as the CHP’s stacks,” explains Herzberg. The buffer ensures that heat is always available to the heat pumps and that the CHP can always dissipate waste heat. It is intentionally way over the required dimension to leave room for expansion and increase flexibility.
For peak-load operation during winter, a 500-kilowatt condensing boiler that was originally installed in 2011 was left in place. Whenever necessary, the boiler can be run on natural gas. Another 1.2-megawatt boiler was removed as part of the renovations since it would have been surplus to requirements.
Optimal usage of hot and cold heat pump sides
Two heat pumps – one installed in 2021 and 2023 respectively – manufactured by Ochsner complement the biomethane CHP. They have an output of 120 kW each and are connected in series. A 5-cubic-meter buffer tank was integrated into the system as well. “Under these conditions, we maximize the cold and hot side of the heat pump loop,” says Herzberg. In the opinion of the expert for energy efficiency at Vereinigte Stadtwerke, this setup significantly raises the overall efficiency of the system.
How does the concept function in reality? The heat extracted from low-temperature coolers of a CHP is usually wasted. It is usually dissipated into the environment by external dry coolers or cooling towers to prevent the fuel mixture from overheating. The Dreiangel facility does not need dry coolers – which is why it is special. “The heat pumps and the buffer tank allow us to minimize heat losses at the LT level,” explains Herzberg.
The ground source heat pumps constantly cool the buffer tank. “In theory, it would freeze at some point,” says Herzberg, “But since the process produces enough LT heat from the ventilation, the engine and the second EGHE, the buffer tank connected to the source-side of the heat pump is practically heated. The excess LT heat is used to heat the buffer tank.” As a result, the ground source temperature is stable between 20 and 30 degrees Celsius no matter the season. According to Herzberg, the COP amounts to an excellent value between 3.5 and 4.5.
Thermal energy produced by the heat pumps is either fed directly into the heating network or into the larger buffer tank where it mixes with the CHP supply flow (90 to 95°C) arriving at a combined supply temperature for the district heating network of about 80°C.
The heat pumps’ electricity demand is partially covered by a 16-kW photovoltaic system installed on the facility’s roof. The system was built by Solar edge and exclusively serves on-site demand.
The heating facility generates about 2,200 MWh of thermal energy annually, the biomethane CHP supplies approximately 1,500 MWh of that total. The rest is produced by the heat pumps as well as the peak load boiler. The modernized system is up and running since autumn 2020. The solar panels were installed in 2023.
This facility, with its combination of heat pumps and combined heat and power system, can serve as an example for other public utilities and suppliers. According to Holger Herzberg, the system exhibits an “ideal synergy between CHP and heat pump”, making it a concept worthy of imitation.